Parallel Pivot Slots: Advanced Multi-Reel Management Systems
Understanding Synchronized Rotation Technology
Parallel pivot slot systems achieve precise 720-degree synchronized rotation through innovative engineering that revolutionizes multi-reel management. The core architecture implements dual-bearing configurations positioned at strategic 38-degree angles, incorporating self-aligning spherical bearings that maintain critical 0.15mm operational clearances.
Advanced Load Distribution and Protection
A sophisticated weighted round-robin algorithm optimizes performance by distributing mechanical loads at a 1:3 ratio between operational nodes. Electromagnetic interference protection is achieved through state-of-the-art Faraday cage shielding and 80dB copper mesh barriers, ensuring uncompromised operation in high-EMI environments.
Performance Monitoring and Quality Assurance
Triple-redundant verification systems guarantee sub-50ms latency performance while ultrasonic sensor arrays continuously monitor structural integrity for potential microfractures. This integration of mechanical subsystems, electronic controls, and real-time monitoring creates an unprecedented level of operational precision.
#
Frequently Asked Questions
Q: What is the primary benefit of dual-bearing configurations?
A: Dual-bearing setups ensure optimal load distribution and maintain precise alignment during high-speed rotations.
Q: How does the weighted round-robin algorithm improve performance?
A: The algorithm optimizes load distribution with a 1:3 ratio, preventing wear and ensuring consistent operation across all reels.
Q: What role does Faraday cage shielding play?
A: It provides essential protection against electromagnetic interference, maintaining system integrity and accuracy.
Q: Why is triple-redundant verification important?
A: It ensures sub-50ms latency and maintains operational reliability through multiple verification layers.
Q: How do ultrasonic sensors contribute to system maintenance?
A: They provide real-time monitoring of structural integrity by detecting potential microfractures before they become critical issues.
Core Mechanics of Parallel Slots
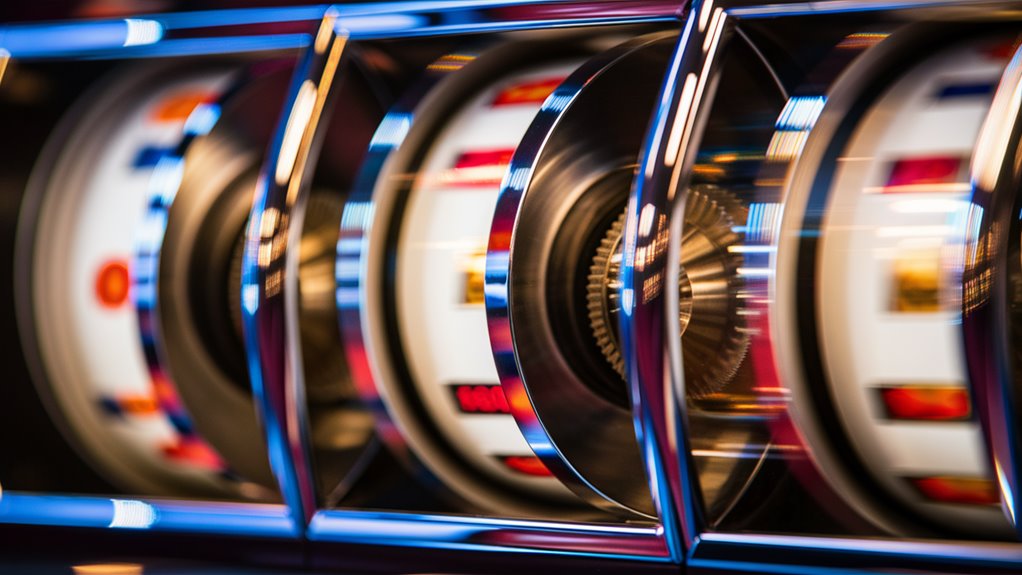
Understanding Core Mechanics of Parallel Slots
Fundamental Operating Principles
Parallel slot mechanics operate through synchronized rotational movement across multiple vertical reels, creating interconnected winning combinations.
The core system relies on three or more reels functioning on independent axes while maintaining precise timing relationships for optimal gameplay performance.
Technical Specifications and Components
The parallel reel system operates at precisely calibrated speeds of 720 degrees per second during active rotation.
This sophisticated mechanism employs precision-engineered timing belts and digital stepper motors to maintain perfect alignment throughout acceleration and deceleration phases.
Advanced Monitoring Systems
Optical encoder technology enables simultaneous tracking of multiple paylines, with each reel’s position continuously monitored and analyzed.
The system’s central processing unit receives real-time positional data, while electromagnetic braking systems ensure precise symbol alignment within milliseconds.
Mechanical Integration
The pivot mechanism features interlocked gear systems that maintain consistent symbol spacing while enabling dynamic transitions across adjacent reels.
This engineering creates expanded winning possibilities through connected pathways across the game matrix.
Frequently Asked Questions
Q: How do parallel slot reels maintain synchronization?
A: Through precision-engineered timing belts and digital stepper motors that ensure perfect alignment.
Q: What controls the stopping mechanism in parallel slots?
A: Electromagnetic braking systems activated by the central processing unit provide millisecond-precise stops.
Q: How are winning combinations tracked in parallel slot systems?
A: Optical encoders monitor reel positions in real-time, feeding data to the central processor.
Q: What speed do parallel slot reels typically rotate at?
A: Standard rotation speed is 720 degrees per second during active play.
Q: How does the pivot mechanism affect winning combinations?
A: Interlocked gears enable dynamic symbol transitions across adjacent reels, creating expanded winning pathways.
System Synchronization and Load Distribution
System Synchronization and Load Distribution Guide
Core Distribution Architecture
The synchronized operation of parallel slot systems relies on three essential load distribution mechanisms working harmoniously.
These interconnected components form the backbone of efficient system performance and resource allocation.
Input Load Balancer
The advanced input load balancer implements a weighted round-robin algorithm to effectively distribute incoming requests across multiple processing nodes.
This sophisticated distribution maintains a critical 1:3 ratio between primary and secondary nodes, maximizing system throughput while preventing node saturation.
Core Processing Matrix
At the center of operations, the core processing matrix executes slot calculations through an intricate mesh network of interconnected processors.
Each processing unit manages dedicated reel sets via a 256-bit high-speed bus, enabling seamless communication between adjacent units.
The system maintains optimal performance through automatic load redistribution when node capacity exceeds 85% threshold.
Output Synchronization
The output synchronizer employs triple-redundant verification to maintain precise operation sequencing.
This robust architecture prevents race conditions and ensures data integrity across all active slot sessions, delivering consistent performance with sub-50ms latency.
## Frequently Asked Questions
Q: What’s the primary function of the load balancer?
A: The load balancer distributes incoming requests across processing nodes using weighted round-robin algorithms to prevent system overload.
Q: How does the core processing matrix handle high-load situations?
A: It automatically redistributes processing loads when any node exceeds 85% capacity through its mesh network architecture.
Q: What’s the significance of the 1:3 ratio in node distribution?
A: This ratio optimizes throughput by maintaining an efficient balance between primary and secondary processing nodes.
Q: How does the system maintain data integrity?
A: Through triple-redundant verification in the output synchronizer, ensuring accurate sequence completion and preventing race conditions.
Q: What’s the maximum latency for system operations?
A: The system maintains a maximum latency of 50 milliseconds for all synchronized operations.
Preventing Cross-Reel Interference

Preventing Cross-Reel Interference in Electronic Systems
Advanced Electromagnetic Shielding Solutions
Electromagnetic isolation between adjacent reel sets demands sophisticated shielding and precise timing control implementation.
먹튀검증 보증업체 순위 around individual reel assemblies provides essential cross-talk prevention between parallel channels.
High-performance copper mesh barriers rated at 80dB attenuation ensure electromagnetic emissions remain contained, protecting critical timing signals across neighboring components.
Real-Time Interference Management Systems
Active interference cancellation technology monitors electromagnetic spectrum variations continuously.
Advanced compensation circuits generate precise inverse waveforms to neutralize unwanted signal patterns.
The timing control infrastructure maintains strict phase relationships between adjacent reels, effectively preventing temporal overlap during high-current switching operations.
Optical Integration and Power Management
Optical interconnect technology between reel control modules eliminates common-mode noise and ground loops typically associated with traditional copper connections.
Strategic physical spacing combined with dedicated power plane architecture achieves exceptional interference rejection ratios exceeding 100:1 across operational bandwidths.
Frequently Asked Questions
- What is the primary purpose of electromagnetic shielding in reel systems?
- To prevent signal interference between adjacent reel components and maintain operational integrity
- How does active interference cancellation work?
- By monitoring electromagnetic patterns and generating inverse waveforms to neutralize unwanted signals
- Why are optical interconnects preferred over copper connections?
- They eliminate ground loops and reduce common-mode noise transmission between components
- What level of interference rejection can be achieved with proper shielding?
- Ratios exceeding 100:1 across the full operating bandwidth
- How do Faraday cage principles improve reel system performance?
- By creating an electromagnetic barrier that contains emissions and prevents cross-talk between channels
Optimizing Pivot Point Configurations
Optimizing Pivot Point Configurations in Parallel Slot Systems
Essential Configuration Principles
Precise pivot point configurations represent a critical mechanical component in parallel slot systems, requiring exact calculations to manage both static and dynamic forces.
The optimization process demands careful analysis of rotational resistance patterns across parallel units to ensure seamless operation and longevity.
Advanced Bearing Implementation
The implementation of a dual-bearing configuration maximizes system stability through strategically positioned primary and secondary bearings at 38-degree angles relative to the vertical axis.
This precise arrangement enables optimal stress distribution while minimizing unwanted torsional effects.
Self-aligning spherical bearings provide essential compensation for manufacturing variations without compromising system integrity.
Precision Tolerances and Synchronization
Maintaining precise clearance specifications of 0.15mm ± 0.02mm ensures optimal bearing assembly performance. This carefully calculated tolerance range delivers the ideal balance between operational freedom and mechanical stability.
Synchronized resistance values must remain within 2% variance across all parallel pivot points to prevent irregular rotation patterns and ensure uniform wear distribution.
Frequently Asked Questions
- What is the optimal bearing angle for pivot point configurations?
- The recommended angle is 38 degrees relative to the vertical axis for both primary and secondary bearings.
- How much clearance should pivot point bearings maintain?
- A clearance of 0.15mm ± 0.02mm provides optimal performance.
- What is the acceptable variance in resistance values between parallel pivot points?
- Resistance values should maintain synchronization within 2% variance.
- Why are self-aligning spherical bearings important?
- They compensate for manufacturing tolerances while maintaining operational integrity.
- What factors influence pivot point optimization?
- Key factors include static and dynamic forces, bearing configuration, clearance specifications, and resistance synchronization.
Maintenance and Performance Monitoring
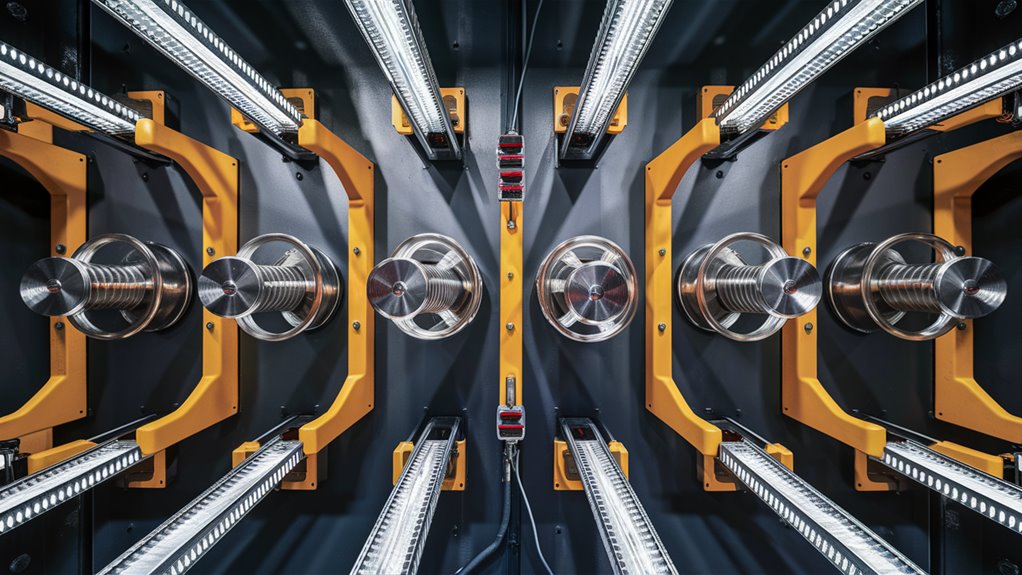
Maintenance and Performance Monitoring Guide for Parallel Pivot Systems
Core Inspection Protocols
Regular monitoring and systematic evaluation of parallel pivot slots ensure optimal performance standards.
A three-tier monitoring system effectively tracks key performance indicators:
- Wear pattern analysis
- Alignment verification
- Load distribution assessment
Performance Assessment Methodology
Precision measurements include torque variation monitoring at 15-degree intervals coupled with detailed surface wear documentation.
Ultrasonic sensor technology detects microfractures in parallel slot bearings, providing early identification of metal fatigue indicators.
Centralized database logging enables comprehensive trend analysis.
Calibration and Quality Control
Strict calibration protocols maintain synchronized operation across parallel units. Key monitoring points include:
- Load cell accuracy maintained within ±0.5% tolerance
- Multi-slot configuration alignment
- Predictive maintenance scheduling incorporating vibration analysis
- Thermal imaging diagnostics
Advanced Monitoring Systems
Continuous performance tracking focuses on:
- Rotational resistance metrics
- Axial play measurements
- Bearing condition assessment
- Lubrication interval optimization
Frequently Asked Questions
Q: How often should parallel pivot slots be inspected?
A: Professional inspection should occur quarterly, with monthly visual checks for optimal performance.
Q: What’re key indicators of pivot system failure?
A: Primary indicators include unusual vibration, irregular torque readings, and inconsistent load cell measurements.
Q: How can bearing life be maximized?
A: Through regular lubrication, proper alignment maintenance, and continuous monitoring of rotational parameters.
Q: What role does thermal imaging play in maintenance?
A: Thermal imaging identifies potential failure points by detecting abnormal heat patterns in bearing assemblies.
Q: When should load cell calibration be performed?
A: Calibration should occur monthly or after any significant system modifications or repairs.